AHU or Air Handling Unit is the device used to process, regulate & circulate the air to the space as a part of Heating , ventilation & air-conditioning System.
It consist of a metal box containing a blowers, filters, Colling/heating coils, humidifier/dehumidifier, dampers etc. We will discuss about each components of AHU one by one in this article.
The conditioned air is supplied to the space/room through sheet metal ducting connected to the AHU Supply outlet port.
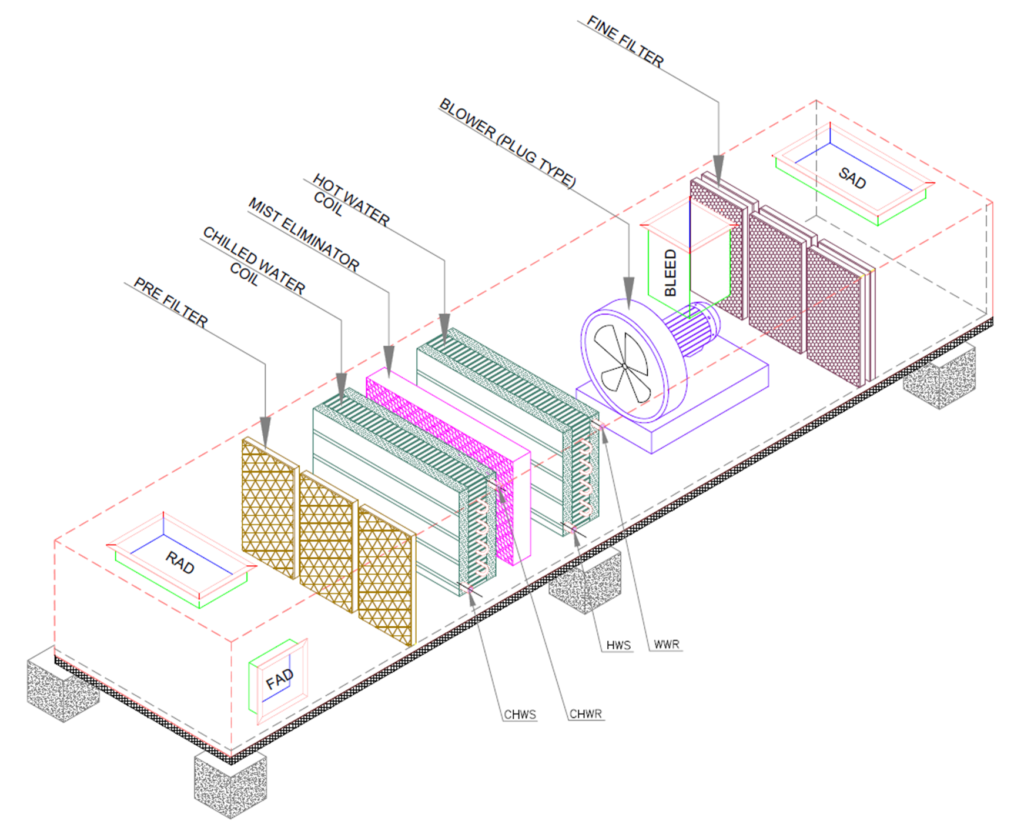
Where you will find the AHU?
- Hospitals
- Malls & supermarkets
- Commercial buildings
- IT companies
- Factories etc.
AHU’s are mostly used in a large commercial buildings where Processed air supplied to multiple areas through ducting with AHU placed in a dedicated room. A single AHU can satisfy the demand of complete floor or more depends on the Heat Load.
AHU Types
According to the mounting position AHU’s are classified as
- Floor Mounted
- Ceiling Mounted/Ceiling suspended (CSU)
Floor Mounted AHU’s are mostly preferred for higher capacity units, while Ceiling suspended AHU’s are used where there is space limitations.
Floor mounted can be of following type;
- Horizontal AHU
- Vertical AHU
CSU’s can not be used for higher capacity requirement instead multiple units can be selected to satisfy the space cooling or heating requirements.
According to the Cooling/heating medium used
- Chilled water/Hot water coil AHU
- DX -Direct expansion coil AHU
Chilled water (CHW) AHU unit coils are usually connected with Chiller or Heat Pump or boiler which supplies chilled or hot water to coil inlet,
whereas the DX AHU’s are connected with refrigerant based condenser units or VRF system which supplies low or high temperature refrigerants to AHU coils.
According to the positioning of Supply Fans
- Draw through type
- Blow through type
The draw-through AHU has a fan which pulls the air through the mixing box, cooling coil and filters before it goes to the ducting work.
The blow-through AHU has a fan which blows the air through the mixing box, cooling coil and filters before it goes to the supply duct work.
Major AHU Components
- Housing (AHU Body)
- Supply Air Fans
- Filters
- Cooling/Heating Coil
- Humidifier/Dehumidifier
- Mixing Box
- Supply/return air dampers
- Supply/return air sensors
- Heat Recovery wheel (special requirement)
1.Housing
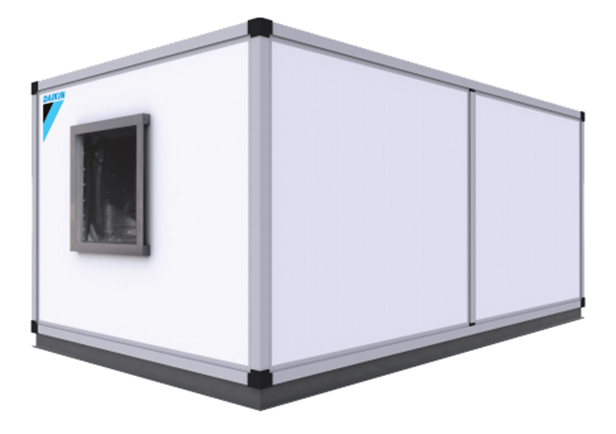
- Its a metal box or external body which houses all the components of AHU inside it. It typically is constructed around a framing system with insulated roofing, flooring, and side panels.
- It is sometimes built in different sections or modules depending on the configuration required.
- Framing system can be constructed from metal c-channels or square steel framing.
- The sides or wall panels can be single or double skin insulated metal panels.
- Sandwich panels are most commonly used with injected polyurethane or fiberglass insulation in between two panel. Internal panel are made of galvanized sheet & external panels are pre painted sheets with thickness of sheet 0.8 to 1mm preferred.
- The floor is typically insulated and covered with a thick metal plate, sometimes in a diamond pattern to assist in providing a walkable surface.
- The roof can be like the sides of the AHU unless it’s in an outdoor application where additional weatherproofing and joint sealing may be required
- •All the metalwork is normally galvanized for long term protection.
2.Blower (Supply Air Fan)
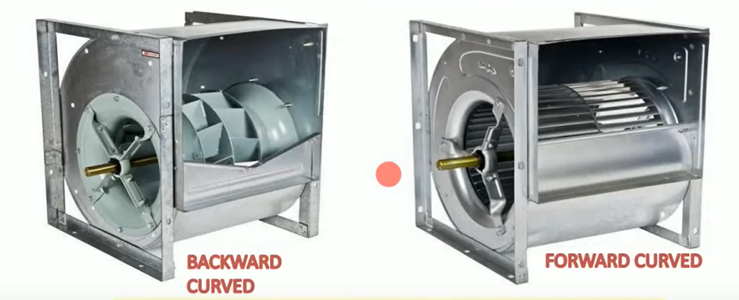
- Purpose of Fan is to recirculate the processed air to the ducting network through which it is transferred to the space to be air conditioned.
- It pulls return air from conditioned space & fresh air from outside so that it can get processed within AHU & recirculated.
- Air handlers typically employ a large squirrel cage blower driven by an AC induction electric motor to move the air.
- The blower may operate at a single speed, offer a variety of set speeds, or be driven by a variable-frequency drive to allow a wide range of air flow rates.
- Some air handlers use a brushless DC electric motor that has variable speed capabilities. •Air handlers in some countries now commonly use backward curve fans without scroll or “plug fans”.
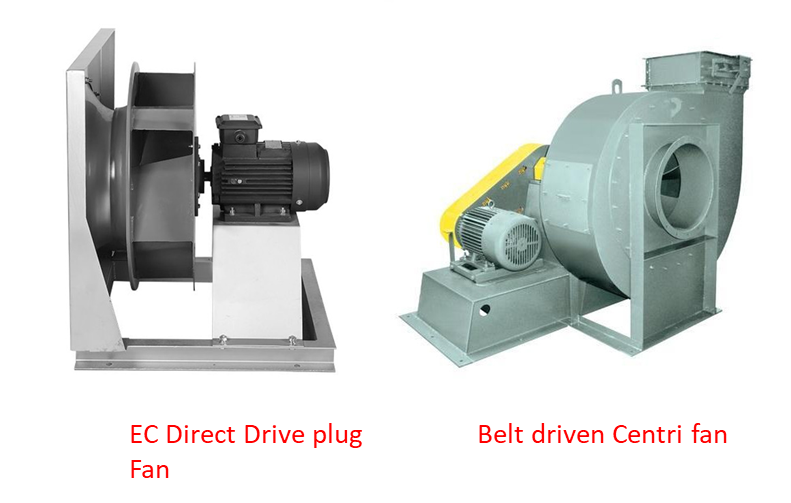
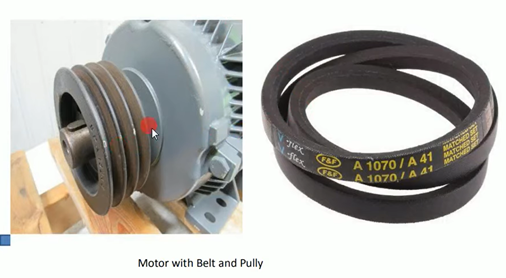
- These are driven using high efficiency EC (electronically commutated) motors with built in speed control.
- Multiple blowers may be present in large commercial air handling units, typically placed at the end of the AHU and the beginning of the supply ductwork (therefore also called “supply fans”). They are often augmented by fans in the return air duct (“return fans”) pushing the air into the AHU.
3.Cooling/Heating Coil
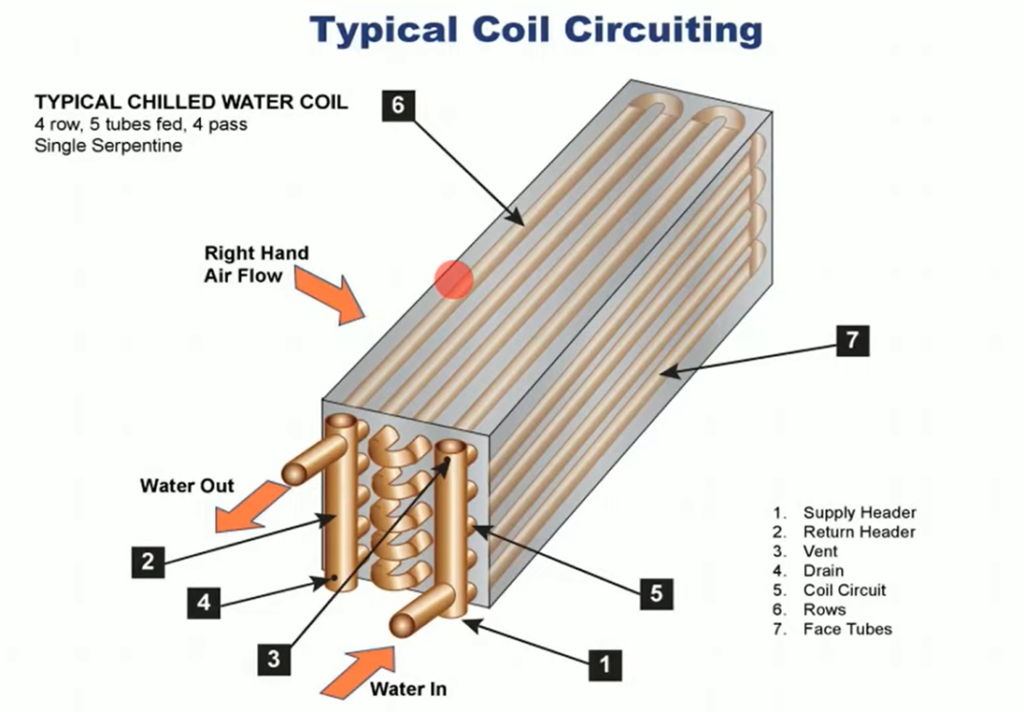
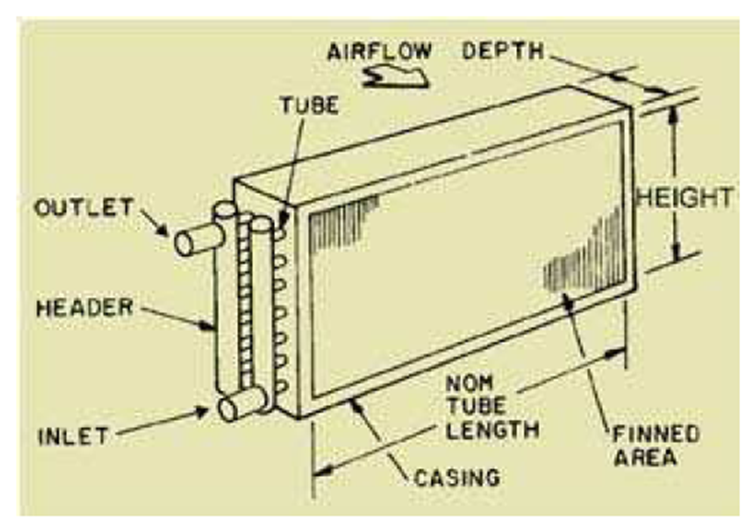
- Most coils found in AHUs are used to provide sensible heating or sensible and latent cooling, and/or in conjunction with humidification and dehumidification.
- Direct heat exchangers(DX) include those for gas-fired fuel-burning heaters or a refrigeration evaporator, placed directly in the air stream.
- Indirect coils use hot water or steam for heating, and chilled water or glycol for cooling
- Coils are typically manufactured from copper for the tubes, with copper or aluminum fins to aid heat transfer.
- The number of rows of copper tubes in the direction of air flow is termed as depth of coil (rows deep). Coils with 3,4,6 or 8 rows are commonly used.
- Fins are arranged perpendicular to the tubes. Fin spacing varies between 8 and 14 fins per inch of tube.
- Plate or ripple fins are used to enhance the heat transfer area.
- For cooling coils, they are built to be piped in a counter-flow arrangement; or, the air flows in the opposite direction as the chilled water (CHW), and/or the refrigerant in DX coils.
- If dehumidification is required, then the cooling coil is employed to over-cool so that the dew point is reached and condensation occurs.
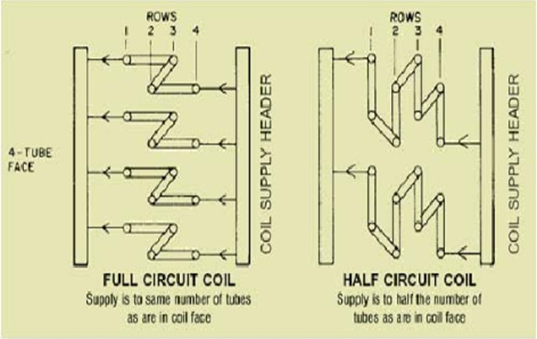
- Number of circuits is the supply given to the no of tubes from main header.
- If the supply is given to alternate tubes in face, we get a half-circuit coil.
4.Humidifier/Dehumidifier
- Humidification is the process of adding moisture to the supply air stream.
- Humidification is often necessary in colder climates where continuous heating will make the air drier, resulting in uncomfortable air quality. Below are the few different types of humidification techniques.
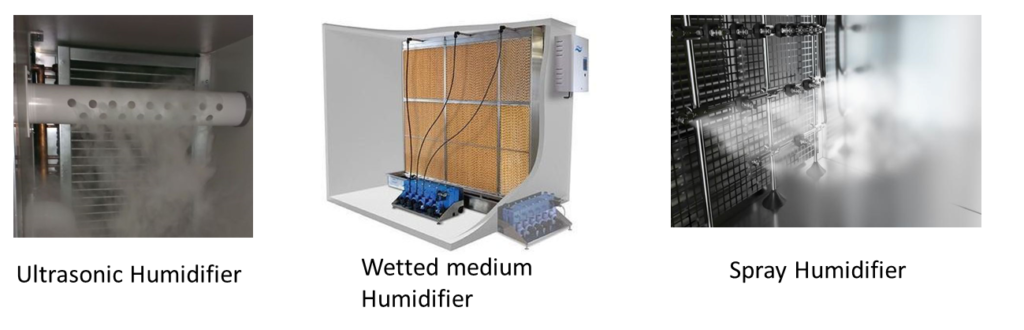
- Evaporative: dry air blown over a reservoir will evaporate some of the water. The rate of evaporation can be increased by spraying the water onto baffles in the air stream.
- Vaporizer: steam or vapor from a boiler is blown directly into the air stream.
- Spray mist: water is diffused either by a nozzle or other mechanical means into fine droplets and carried by the air.
- Ultrasonic: A tray of fresh water in the airstream is excited by an ultrasonic device forming a fog or water mist.
- Wetted medium: A fine fibrous medium in the airstream is kept moist with fresh water from a header pipe with a series of small outlets. As the air passes through the medium it entrains the water in fine droplets. This type of humidifier can quickly clog if the primary air filtration is not maintained in good order.
- Dehumidification is the removal of moisture from the air stream before supplying to the space to maintain appropriate level of humidity.
- Popular methods of dehumidification are by Condensation or using Desiccant dehumidifiers
- Condensation: If dehumidification is required, then the cooling coil is employed to over-cool so that the dew point is reached and condensation occurs. A heater coil placed after the cooling coil re-heats the air (therefore known as a re-heat coil) to the desired supply temperature. This process has the effect of reducing the relative humidity level of the supply air.
- Desiccant dehumidifiers:

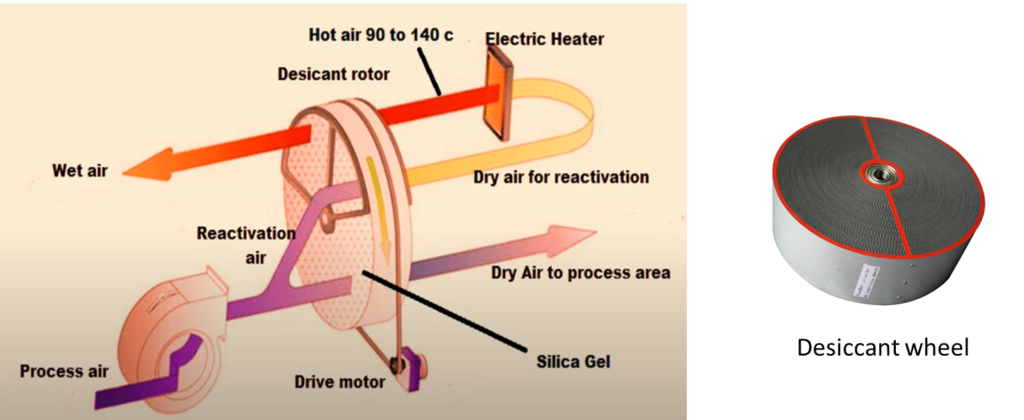
- This dehumidifiers use a patented desiccant wheel, where air passes through the flutes of the material , contacting the desiccant.
- Incoming process air gives off its moisture to the desiccant absorber (usually Silica or lithium chloride), and is dry as it leaves the wheel.
- The humidity-laden wheel rotates slowly into a second, smaller airstream which has been heated.
- This smaller exhaust airstream, known as reactivation air, warms the desiccant. The warmed desiccant gives off its moisture which is then carried away by the reactivation air.
- The newly dried desiccant material is rotated back into the process air, where it absorbs moisture once again.
5.Filters
- Air handling unit (AHU) filters are used in an HVAC system to prevent dust and other contaminants from circulating in a building. They help improve indoor air quality (IAQ), which has become an increasingly important concern for all facilities since poor IAQ negatively impacts people’s health and productivity.
- In applications with more than one set of filters, a preliminary or rough grade filter would be provided first in the direction of airflow which removes large dust particles conveniently.
- Intermediate and/or final filters, where provided, will be of varying grades of filtration or efficiency to assist in removing smaller and smaller contaminants.
- Filters are rated by ASHRAE Standard 52.2 – 2012 test methods and classified by minimum efficiency reporting value (MERV).

- Nearly all AHUs will have a MERV 7 or 8 filter assembly.
- A hospital inpatient care application would also use a MERV 15 with greater than 95% efficiency
- A cleanroom would use MERV 20 at greater than or equal to 99.999% on 0.10 to 0.20 micron particles.
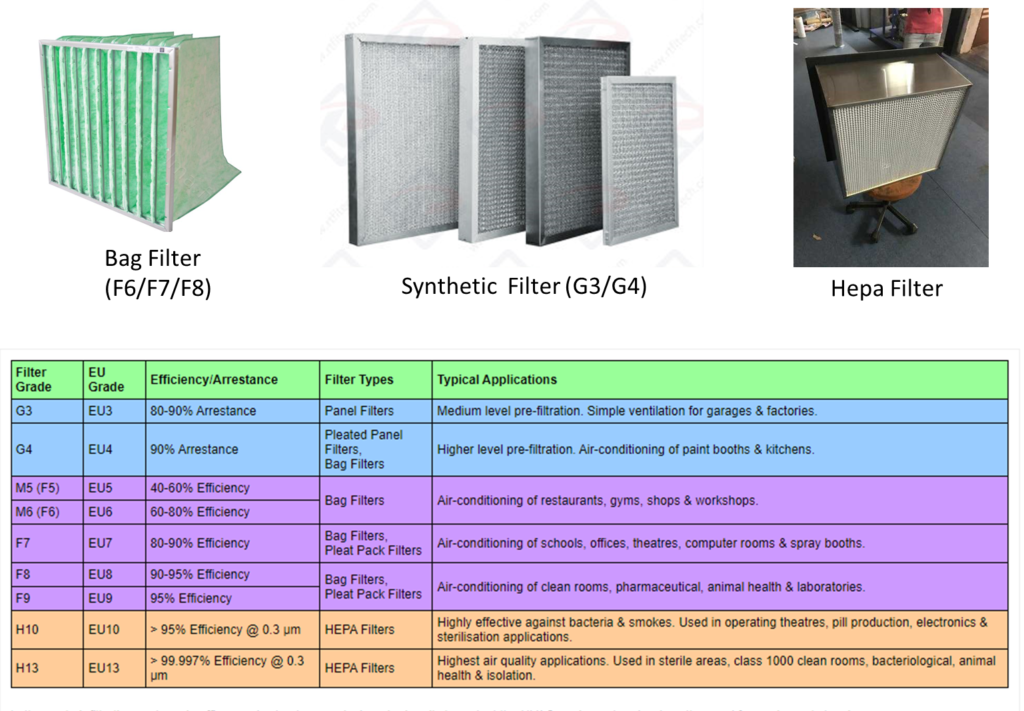
- High efficiency Particulate Air filter HEPA* : Has efficiency 99.97% of particles in the 0.3-micron range. Particles that are larger or smaller than 0.3 microns are captured with a greater than 99.97% efficiency. Mostly used in operation theaters, clean rooms and laboratories etc.
6. Dampers & mixing chamber
Mixing Box: In order to maintain indoor air quality, air handlers commonly have provisions to allow the introduction of outside air into, and the exhausting of air from the building. A mixing chamber is therefore used which has dampers controlling the ratio between the return, outside, and exhaust air
Outside Air Damper (OA): to regulate flow of fresh outside air entering the AHU Mixing Box.
Return Air damper (RA): to regulate flow of return air entering the AHU Mixing Box.
Supply air damper (SA): to regulate flow of Supply air to the space.
Bleed Air damper : to bleed of excess air out of ahu to maintain proper air balance.
Dampers are usually integrated with motorized actuator to have proper air balancing with respect to system air flow requirement.
7. Sensors & other accessories
- Temperature sensors at supply & return air: It indicates the cooling load requirement of particular space & signals the motorized valve to adjust chilled/hot water requirement of coil, thereby increasing system efficiency.
- Differential Pressure switch: used to sense airflow status across the fans, dirty status across the filters in air handling unit.
- Low limit temperature controllers protect hot and/or chilled water coils from excessively low temperatures.
- High and low limit static pressure controllers prevent fan housings and ductwork from pressure extremes.
- Fan vibration switches monitor for excessive fan vibration.
- Duct Smoke detectors monitor for smoke in the airstream.
All of these controllers are used to protect the equipment in the event of abnormal system operation. Safety devices such as these are typically electromechanical or electronic in nature, and the setpoint or “trip” point adjustment is integral to the device.
other accessories used are
1.Drain pan: The condensate drain pan catches all that humidity and excess water that is removed from your air through coil. It also makes sure the water is safely disposed of outside the AHU room.
2.Spring ant vibration mounts: To absorb the vibration of fan motor.
3. Inspection window, Lamp holder , switch etc.
8. Heat Recovery Wheel or plate
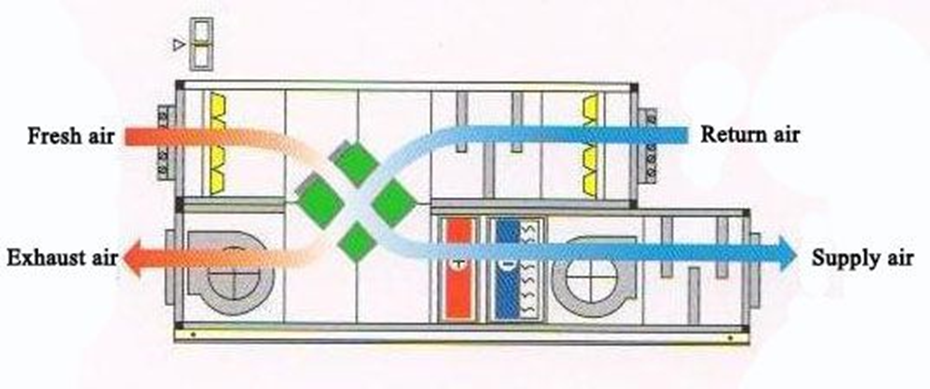
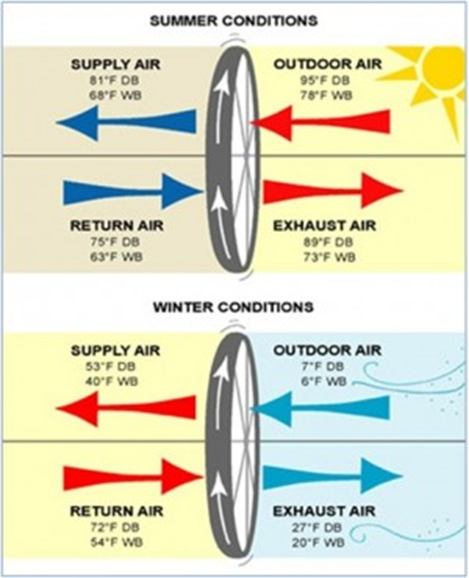
- Heat recovery is preferred if any re-circulation of air in system is undesirable.
- Energy from waste return air before getting exhausted is used to cool or heat the fresh air entering the ahu through heat recovery system.
- The fresh air & return air are completely isolated or no moisture or odors can be transferred.
- The heat recovery system may be plate type or wheel type.
- Aluminium or polymer plates are used
- Wheel used are called Heat recovery wheel/enthalpy wheel/thermal wheel.
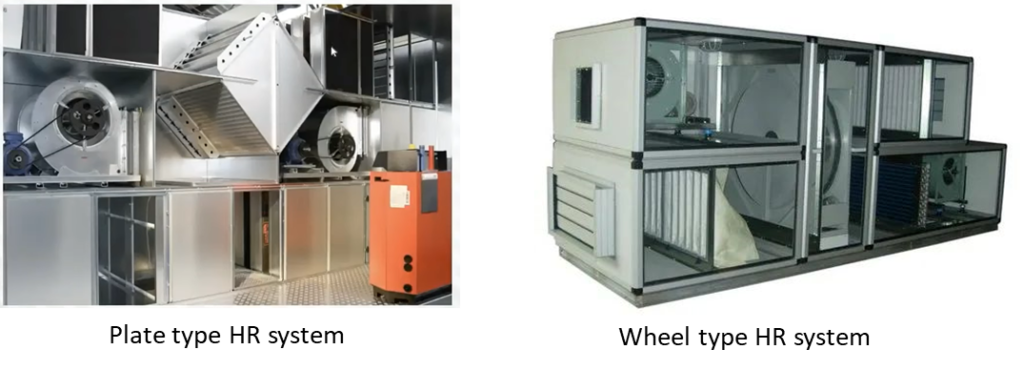
- Most energy recovery devices transfer heat (sensible) energy only. An Enthalpy Wheel allows both heat (sensible) energy and moisture (latent) energy to be exchanged.
- The Enthalpy Wheels are usually made of porous materials to increase surface area which aids in energy transfer. In most cases a matrix core material is coated with a desiccant such as Silica Gel or other molecular sieves to increase latent transfer.
The AHU may or may not contain all of the components as describe above. The selection of components is purely based on application & requirement of end user.
Though Blower, cooling coil & filters along with necessary dampers are the major components used in almost all application.